Peerless Precision Provides Unique Capabilities for Optical Machining
Optical measuring systems and 3D measuring systems are expected to consistently deliver extreme accuracy and precision. To do so, the internal parts and components in these devices must be reliably manufactured to extremely tight tolerances. Parts that aren’t made to the exact required specifications can result in tolerance stacking and lead to significant reading errors and improper function of the optical equipment.
When this kind of complexity is involved, you need a shop that has optical machining experience to make sure the job is done right.
At Peerless Precision, we have more than 40 years of experience in custom optical machining. Our technical experts can manufacture optical measuring equipment parts of any shape or complexity. We’re one of a handful of precision machine shops in the U.S. that is capable of creating the internal parts and components required for 3D measuring systems and larger-than-life microscopes.
Peerless Precision Knows Optical Machining
We work with tough materials. At Peerless Precision, we’re not afraid to work with tough materials—titanium, tungsten, and even invar—that are used in optical machining.
Many shops try to avoid using these materials, which can be difficult to work with and hard on tools and machines (earning their reputation as “chewy”). We’ve got both the tools and the expertise to offer these capabilities. We also rely on tooling suppliers’ advice on how to best machine unusual materials, maintain the long life of our tools, and run our machines with maximum efficiency. That’s how we keep our costs (and our quotes) down and our lead times as short as possible.
We’re experts in thin wall machining. Some of the components in optical equipment are as thin as tin foil. We’ve got the capabilities to create thin walls, even from challenging materials like titanium, that are just .003” thick.
We achieve extremely tight tolerances. Technically, a part is considered to have a tight tolerance if its permitted variance is +/- .002-.001 inches. Due to its precise measurement systems, optical machining requires much tighter tolerances than standard machined parts. . At Peerless Precision, we’re able to achieve extremely tight tolerances ranging from .0001”-000005”.
We know cosmetic appearance is crucial. We have an extremely high level of quality for the aesthetics of our customer-facing parts. We make sure there are no nicks, dings, scratches, fingerprints, or discolorations. During inspection, we hold the parts under a light that is as bright as the sun to ensure they are pretty, shiny, and perfect. If you line 10 components up on a shelf, all 10 will look identical.
Case Study: Coldfinger Weldments
Coldfinger (coldwell) weldments are a critical mechanical component for optical machining. We currently manufacture coldfinger weldments that are used in submicro cryogenic cooling systems for infrared, night vision, and thermal imaging equipment.
The weldments we make consist of two separate components, base and end cap, which are individually matched prior to welding. In order to match, there can’t be a gap between the two components: they must be able to come together with a light press fit so the end cap won’t fall off of the base if it’s inverted. Using a light press fit also keeps the components from fitting too tightly, which could cause a distortion of the internal diameter after the welding process.
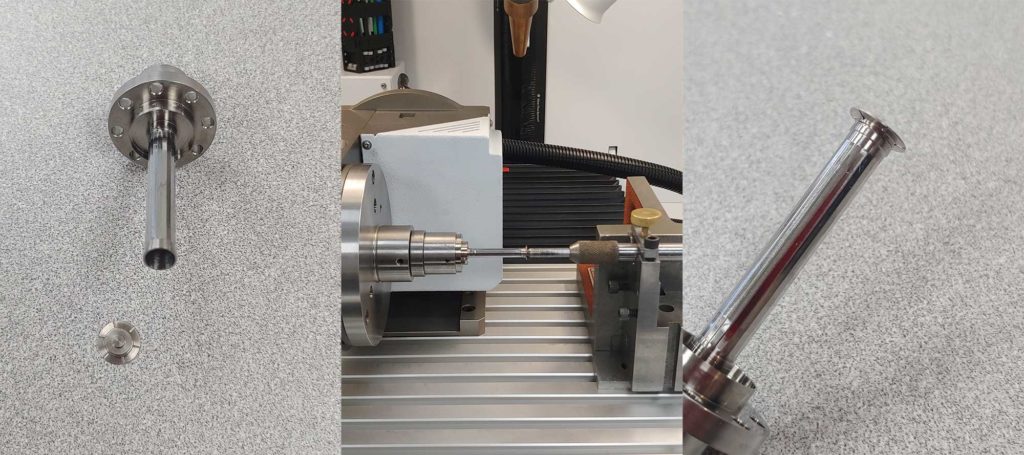
(left to right): base and end cap, setup for laser welding, welded parts (Images:
Not only have we been making coldfinger weldments for more than 20 years, we even purchased a laser welder specifically to weld these components and further expand our capabilities for optical equipment.
When it comes to optical machining, there’s no substitute for quality and experience. Request a quote from us for your next commercial optics project.
Comments are closed